Vibration Testing Services: (<<< image above is the old style image)
- Are You Ready to Resolve Your Machinery Reliability Problems? (<< drop down to include the following)
If so, contact our expert teams at Vibration Analysts Inc. for comprehensive yet economical solutions for your vibration program. Vibration programs help minimize machinery downtime while maximizing life and reliability, increasing plant production to new heights. Find out how our expertise and free 24/7 technical support make the difference!
- Our Philosophy (<< drop down to include the following … down to “Benefits of Choosing VAI’s Services’
We provide machinery vibration testing services using state-of-the-art vibration test equipment and our patented data analysis process delivers exceptionally accurate data analysis results. At VAI, machinery vibration data analysis is our core service and since our survival depends on keeping our clients happy, we only use the industry’s best test equipment and software made by Emerson Process / CSI.
Think of it this way:
- The PARAMOUNT requirement of any vibration program is that it detect and identify machinery faults and degradation at the earliest possible stage so that timely corrective action can be implemented to prevent failures.
- The health of your plant machinery health will only be as good as the data analysis process
- The data analysis will only be as good as the data that’s been collected
- The data that’s been collected will only be as good as the test equipment used to collect it
- The test equipment will only function as good as the software that programs it
- VAI only uses the industry’s best rated vibration test equipment and software made by Emerson Process / CSI
- VAI offers total program support and oversight which provides clients with the most accurate and affordable vibration programs possible.
Our clients can also save a substantial amount of money by collecting their own data and we provide FREE on-site Data Collector Training using the industry’s state-of-the-art vibration test equipment. Clients collect their data, and we analyze it. It’s THAT simple and economical.
- Benefits of Choosing Our Services (<< drop down to include the following)
Choosing our services means your company is now partnering with the industry’s leader in machinery vibration analysis and vibration program support. Our company is committed to providing excellence and unprecedented customer service with every project. At VAI when a client has a vibration problem, it’s also OUR problem 24/7 until it’s been resolved. That means we’re ‘with you’ on weekends, holidays and off-hours. If you have a vibration problem, it’s also our problem until it’s been resolved to your satisfaction.
VAI offers clients several unique benefits, especially for industries that rely on the health and reliability of their products. Here are just a few key benefits:
- Quality Assurance: (<< Include this bullet under “Benefits of Choosing Our Services, and include the following as a drop down)
Vibration testing is vital to providing quality and durability of products, machinery and maintaining equipment health. VAI’s vibration testing services provide a comprehensive assessment which identifies potential degradation, structural and piping weaknesses (bending modes), design flaws, or material issues (cracked welds, excessive unbalance, lubricant issues) that may arise at various times and under different machinery operating conditions.
- Product Validation:(<< Include this bullet under “Benefits of Choosing Our Services, and include the following as a drop down)
Our vibration testing services can be used to validate products under real-world conditions. This is particularly important for industries such as the automotive, aerospace, electronics, and manufacturing plants, where vibrations can occur during transportation, operation, or other processes.
- Compliance with Standards:(<< Include this bullet under “Benefits of Choosing Our Services, and include the following as a drop down)
VAI is able to work with nearly all industrial standards and regulations. We have experience testing machinery to DOD Mil specs and NRC requirements. During testing, we can determine if machinery meets or fails these standards. We can also provide guidance towards resolving vibration issues by recommending precision balancing, bearing replacement, structural stiffening, resonance detuning (changing mass or stiffness) and much more.
- Customized Testing Protocols:(<< Include this bullet under “Benefits of Choosing Our Services, and include the following as a drop down)
Our vibration testing services can be modified to develop customized testing protocols based on the specific needs of a client’s product or industry. This will support targeted evaluations that address the unique challenges and requirements of a particular product.
- Cost Savings:(<< Include this bullet under “Benefits of Choosing Our Services, and include the following as a drop down)
When applied early in the development phase, vibration testing services can lead to significant cost savings by minimizing expensive recalls, unnecessary maintenance repairs, as well as warranty claims due to faulty products.
- Accelerated Testing:(<< Include this bullet under “Benefits of Choosing Our Services, and include the following as a drop down)
VAI’s experience includes using ‘shaker tables’ to simulate a wide range of environmental conditions, such as submarine and surface ship vibrations caused by propellers, and on/off highway vehicle vibrations. This method of testing accelerates the ‘aging’ process, allowing manufacturers to quickly assess the long-term effects of vibration induced fatigue failure.
- Improved Product Design:(<< Include this bullet under “Benefits of Choosing Our Services, and include the following as a drop down)
VAI’s vibration testing services includes ODS testing which can be used to refine and improve machine / structure / piping system designs. This type of testing helps engineers create more robust and reliable products, reducing the likelihood of failures in real-world applications.
- Customer Confidence:(<< Include this bullet under “Benefits of Choosing Our Services, and include the following as a drop down)
VAI’s vibration testing services can add credibility and instill confidence in end-users by demonstrating the supplier’s commitment to verify the quality and reliability of their products.
- Research and Development Support:(<< Include this bullet under “Benefits of Choosing Our Services, and include the following as a drop down)
VAI’s expertise can be a valuable resource when optimizing products, materials, and manufacturing processes to withstand background vibration energy and we are willing to collaborate with other businesses during the research and development phase to ensure the maximum product quality and reliability.
- Benefits of Vibration Testing (this should be a major bullet (#3) after “Our Philosophy’. Copy everything from ‘Early Fault Detection’ thru ‘Data Based Decision Making’ under it)
- Early Fault Detection
- thru
- Data Based Decision Making
- Early Fault Detection
- Types of Vibration Tests (this should be bullet #4 after Benefits… Copy everything from ‘Acceptance Testing thru Resonance and Critical Speed’ under it)
- Acceptance Testing
- thru
- Resonance and Critical Speed Testing
- Acceptance Testing
Photos at the end are good. Will add words to explain the photos later.
Benefits of Vibration Testing
- Early Fault Detection: (<< include the following as a drop down)
Periodic data collection testing serves as a crucial tool in monitoring machinery health, offering trend data in the form of spectra and waveform analysis. This data enables the detection and identification of subtle changes in machinery vibration energy, often indicative of early stages of degradation, abnormal operating conditions, or inadequate maintenance practices. By detecting these changes early on, clients can implement prompt corrective or proactive maintenance measures, mitigating the risk of catastrophic failures and minimizing downtime. Ultimately, leveraging periodic data collection testing empowers businesses to optimize equipment reliability, enhance operational efficiency, and safeguard against potential disruptions.
- Precise Diagnostics: (<< include the following as a drop down)
By analyzing periodic trend data, VAI’s Category IV Analysts can provide a more accurate and detailed report about the nature and severity of machinery vibration issues. VAI’s advanced vibration testing services can identify specific machinery faults thereby giving clients timely and accurate recommendations for making repairs and replacements. A focused approach helps reduce unnecessary maintenance work compared to the usual ‘shotgun approach’ offered by many competitors which is, inspect and repair ‘everything’.
- Condition Monitoring:(<< include the following as a drop down)
Condition monitoring is the process of periodically (or continuously) monitoring machinery health and performance to detect and identify deviations from normal operating conditions. When detected in the earliest stages, corrective actions can be implemented before these issues degrade, possibly causing a failure. This approach gives Maintenance time to make repairs, and with the least amount of cost to the plant. For example, replace a motor bearing now, or replace the entire motor later. By periodically (monthly is recommended) collecting and analyzing machinery vibration data, clients can optimize their maintenance schedules, improve machinery reliability and its operating life, and enhance its overall efficiency and possibly plant production.
- Machinery Performance Optimization:(<< include the following as a drop down)
By using VAI’s vibration testing services, you can gain insights into many machinery health conditions. This includes machinery reliability, performance, efficiency, and alignment. By optimizing machinery operating conditions, clients can improve energy efficiency, reduce operational costs, and enhance operating life and reliability to the plant.
- Root Cause Analysis:(<< include the following as a drop down)
VAI’s vibration testing services are not only instrumental in detecting machinery issues but also in facilitating in-depth root cause analyses for clients. By accurately identifying and addressing the root cause of failures, clients can effectively prevent recurring problems, thereby maximizing the long-term operating life and reliability of their equipment to support uninterrupted plant operations. This proactive approach not only minimizes downtime and associated costs but also enhances overall operational efficiency and ensures sustained productivity in the long run.
- Customized Maintenance Strategies:(<< include the following as a drop down)
VAI’s vibration testing services are tailored to support client maintenance strategies by taking into account the unique characteristics of their machinery. By leveraging our experience with our vibration testing services, clients can optimize the effectiveness of their maintenance activities while simultaneously minimizing costs and downtime. Whether it’s predictive, preventive, or proactive maintenance, our comprehensive analysis helps clients make informed decisions and prioritize actions to ensure optimal performance and reliability of their equipment. This strategic approach not only enhances operational efficiency but also fosters a proactive maintenance culture, ultimately driving long-term cost savings and maximizing asset up-time.
- Risk Mitigation:(<< include the following as a drop down)
By determining the normal vibration levels and frequencies of critical components under normal operating conditions, VAI can quickly detect and identify any degradation due to wear, abnormal operating conditions, and improper or incomplete maintenance. By proactively addressing these changes, VAI can help prevent irreparable machinery damage or failures.
- Compliance with Industry Guidelines:(<< include the following as a drop down)
VAI’s vibration testing services aligns with established industry guidelines and best practices. By adhering to these industry ‘expectations’, we ensure your machinery or structures adhere to pertinent safety and reliability standards, enhancing overall operational integrity. We have also ‘raised the ladder’ when it comes to classifying rolling element bearing defects based on their waveform impact levels and the fact that rolling element bearings degrade at an increasing rate. We’re also working on a classification chart for bearings that are operating with ‘ball skid’ type of defect.
- Data Based Decision Making:(<< include the following as a drop down)
By applying VAI’s patented vibration data analysis process, we can make very informed recommendations which enable clients to allocate resources effectively, prioritize maintenance tasks, and make strategic improvements to enhance overall system performance.
- Types of Vibration Tests (includes the following)
-
- Acceptance Testing
- Starting up a New Plant? Putting new equipment into service? Need to qualify new or refurbished equipment from suppliers?VAI has highly qualified ISO Certified Category IV Analysts who can perform accurate and comprehensive acceptance tests to meet your requirements. We do more than just collect one data set and call it good. We will support and witness all acceptance testing and perform according to specified operating conditions. We support Acceptance Testing that includes coast up / coast down, natural frequency, resonant and “bump” testing, multiple data sets at specified operating conditions, and speed and operating condition variation. We will also include a customized and detailed report documenting all data taken, along with results, recommendations and conclusions.VAI’s Certified Vibration Analysts know how to perform accurate and comprehensive acceptance tests that will meet your specification requirements. We will also witness and ensure acceptance tests are performed in accordance to specified operating conditions. This includes start-up and coast-down tests, natural frequency and resonant “bump” testing, variable speed tests, collecting multiple data sets at different operating conditions including variable load / speed / and temperatures. We also provide detailed reporting and will include all data plots, test results, conclusions, recommendations and photos where allowed.
- Acceptance Testing
-
- Balance Testing
- Our Vibration Analysts can perform single plane fan balancing, which may be needed when amplitudes get too high at operating speed. In nearly all cases, the radial vibration levels will be noticeably higher than the axial levels.For safety reasons, VAI advises against untrained staff performing the balancing procedure. This is because if a balance weight should loosen and come off during the procedure, the kinetic energy can be extreme if not lethal and possibly damaging the component.VAI’s Certified Vibration Analysts can perform precision balancing because they have been highly trained and certified. There is no need to purchase expensive vibration test equipment or balancing software; our Vibration Analysts will do everything except turn wrenches (due to insurance concerns).
- Balance Testing
-
- Baseline Testing
- After the Acceptance Tests are completed at the supplier’s facility, it’s always wise to ensure Baseline tests are performed at your facility with the equipment properly installed and at specified operating conditions. By performing Baseline testing, VAI can determine if any damaged occurred during shipment (impacted bearings), whether the machine is properly alignment, and whether there are any localized resonances that will increase ‘normal’ operating vibration levels. It’s always a challenge for both the supplier and the buyer when the Acceptance Test levels are low, but the plant installed levels are high, but we can help troubleshoot these issues and provide recommendations.
- Baseline Testing
-
- Fault and Condition Testing
- All rotating machines produce operating frequencies and amplitudes that are unique to each machine, but given all the frequencies, how do you know which ones are normal or not, and if not, how bad are they? That’s where our decades of experience with different components come in handy. We can test for impacted bearings, unbalance, misalignment, motor air gap, pump vane pass, worn or degraded gears and so much more. Our services are particularly important when critical machines develop high vibration levels that may cause a failure, reducing or shutting down plant production.
- Fault and Condition Testing
-
- Multi-Channel Testing
- Sometimes multi-channel testing is needed to determine the effects when operating conditions (temperatures, rpms, load, pressure) are changed. We can collect continuous high resolution vibration data over extended periods (hours, days if needed) to determine the effects of these changes, and we can do this on up to 16 channels simultaneously.
- Multi-Channel Testing
-
- ODS / Modal Analysis Testing
- Our comprehensive ODS (Operating Deflection Shape) Testing supports a detailed analysis of machinery operation under operational conditions, providing insights into structural dynamics, resonance frequencies, and mode shapes. This enables clients to identify potential issues such as excessive vibration or misalignment, and implement targeted corrective measures. By performing an ODS test, clients can troubleshoot the most difficult of vibration issues because the animations produced by an ODS test show how the machine is operating in real time and at any desired frequency.
- ODS / Modal Analysis Testing
-
-
- ODS testing consists of three main steps:
- Building a 3-D model of the machine / structure / system using dedicated software.
- Collecting x, y and z vibration data at each point within the model
- Meshing the data so the model moves as a complete ‘assembly’ at a frequency.
- The results of an ODS test provide a visual 3-D animation showing how a machine moves in real time at any frequency. The benefits of this type of test include:
FOR SOME REASON I CANT GET THIS AREA TO CONDENSE with one line of spacing. Tried NOTEPAD. I keep making it worse
- By collecting ODS data under actual operating conditions, the ODS animation can identify issues such as misalignments, unbalanced components, and structural weaknesses. For example, VAI determined that the mounting pedestal under a 90-degree safety related gearbox, was moving erratically. Upon closer inspection, we determined the gearbox casing was approximately 1/2” thick, while the mounting pedestal under it, had only ¼” walls .. AND it had two (2) large openings to support coupling maintenance (the weak link was UNDER the more massive and rigid gearbox).
- ODS testing provides animations that show how machinery or structures respond to different operational loads. This data can be used to modify system strength, optimize machine performance, improve efficiency, and enhance the overall reliability of the machine.
- In the case of unexpected vibrations or performance issues, ODS test data helps to identify the root cause(s). This information is valuable for troubleshooting and implementing corrective measures.
- By understanding the dynamic response of machines and structures, ODS testing can aid us in developing effective preventive maintenance plans. Maintenance activities can be scheduled based on actual operational conditions and run-times, reducing downtime and maximizing machinery life.
- ODS testing can also be used during the design and manufacturing process to validate the structural integrity and dynamic behavior of components and structures. It ensures that the equipment meets design specifications and quality standards.
- ODS testing can help identify dynamic issues that might reduce the overall safety of machinery and structures, thereby helping to prevent catastrophic failures that could pose safety risks to personnel and the plant.
A visual model of how the assembly is moving. Consider a metal I-beam that has a vertical crack in the middle of the beam. While this defect may not be readily apparent, the 3-D model when activated, will exaggerate the beams deflection, clearly showing an anomaly where the crack is, leading inspectors directly its location. ODS testing also provides insights into natural frequencies, mode shapes, and dynamic responses of how machines and structures move. ODS testing is however, labor intensive and a simple model may have over to 100 points. Since x, y, z data must be collected at each point, that’s a lot of data collection!
- ODS & Modal Analysis tests are very similar, however during ODS testing the machine self-generates the vibration energy needed to create the animation. On the other hand, Modal Analysis testing uses manual labor to generate the vibration energy, which is why ODS testing is preferred. Even so, ODS and Modal Analysis tests are very labor intensive, which is why all other testing should be performed first.In summary, Operational Deflection Shape testing provides a slow motion, exaggerated 3-D animation of how a machine or structure is moving. This allows clients to implement corrective maintenance, perform necessary optimizations, and enhance machine / structure reliability.
- ODS testing consists of three main steps:
-
-
-
- Modal Analysis Testing is different in that the Analyst uses ‘modal hammers’ to excite the vibration necessary which generates 3-d animations showing the machines expected movement. To date, VAI has determined that ODS testing is the preferred method simply because it provides the energy to create the data (much easier than wielding modal hammers).Unless a machine vibration is excessively high (potential of failure during the test period) the ODS test may be the preferred test. Contact VAI for more information.
-
-
- Resonance & Critical Speed Testing
- We can also perform resonance tests on structures, systems and components to determine if any of the normal and expected forcing frequencies can excite a resonance. If the machine is not motor driven, and can be slowly ramped up and like (like a turbine driven pump) we call collect start-up and coast-down data to determine which rpm(s) the operators should avoid operating the machine at.
- Resonance & Critical Speed Testing
One of our clients, a company with 45 plants across the US and Mexico, reported an ROI of $6.38 for every $1.00 spent on VAI’s services. In fact, by averting just one (1) critical machine failure, clients can save enough money to pay for their vibration test equipment. For more information, please contact us at 815-742-1793.
ODS ANIMATION OF PIPE RESONATING A PUMP VANE PASS:
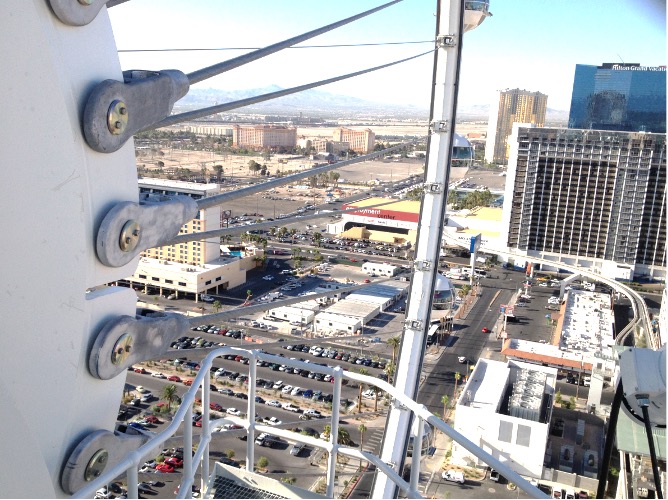
VAI Testing the Caesar’s High Roller in Vegas